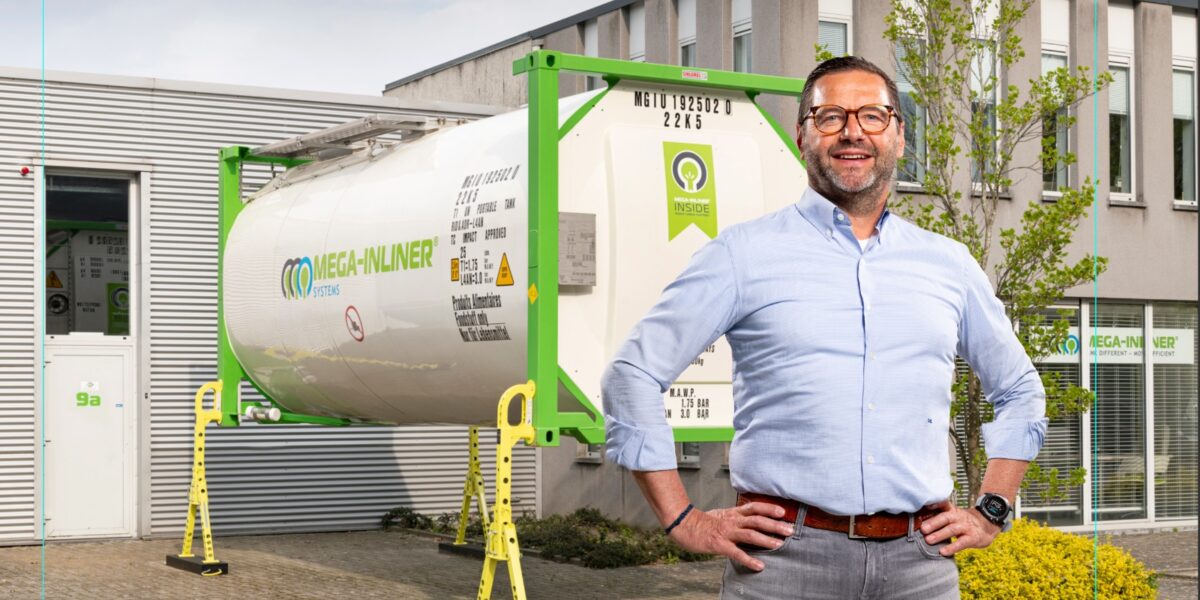
‘Reduce residue in tanker transport to minimum’
With cocoa quotations at record highs, no chocolate company wants to waste cocoa. Every cocoa bean must be saved. Mega-Inliner International Group jumps on this with a patented solution. ”Because the chocolate sticks to the inside, there is much more residue with conventional tanks.”
It started in 2016, when Mega-Inliner International Group was founded with the idea of transporting beer in bulk, without concessions on quality. ”In short, it comes down to a large food-grade bag that sits inside a tank container,” explains Coen de Lange, former innovation consultant in logistics and co-owner of Mega-Inliner. “This gives you much more control over the quality and temperature of the beer. The inliner prevents the entry of oxygen and the exit of CO2. The tank is emptied with air pressure instead of CO2 or pump. The challenge was to make a large 25,000-litre bag, which we eventually succeeded in doing. Big brewers like AB InBev, Heineken and Grolsch are starting to switch to this system, Coca-Cola also already used it.” From there, De Lange continued to look at how the patented solution could be applied to other food products, such as liquid oils and fats, fruit juices, as well as chocolate.
Cocoa prices are at record highs. How can you help companies save chocolate?
”Instead of transporting the chocolate directly into the tank, our system pumps the hot liquid chocolate into the bag. This minimises chocolate loss, as almost all chocolate can be squeezed out of the bag when emptying. This is in contrast to conventional tankers and tank containers, where the chocolate is transported without a bag and the chocolate loss is much higher.”
How much chocolate does your product save?
”Because the chocolate sticks to the inside of the tank, with normal tanks without bags there is much more residue, up to 300 kilos per load. With us, 35 to 50 kilos of chocolate remains in the bag, but also this residue can still be put to good use. After solidifying, the chocolate can be easily removed from the bag, so then you have no loss at all.”
Which companies are interested in your system and why?
“Within the cocoa market, shippers are still ‘unconsciously incompetent’ when it comes to the Mega-Inliner® System. Unlike other food sectors, we still have limited awareness within the chocolate sector, which is why we are working on getting this done. We are already in talks with chocolate companies like Cargill and Barry Callebaut and they are interested. What drives them are the benefits of less chocolate loss and CO2 reduction combined with quality assurance within the total logistics chain. We also eliminate the risk of cross-contamination with previous loads. The product never comes into contact with the tank and therefore never with previous contents.”
How does your price compare with that of conventional transport methods?
”The total cost is always lower compared to conventional tanks. This is because conventional tanks have to be cleaned, which is not required by our Mega-Inliner tanks. So no cleaning costs and no extra CO2 emissions from the extra empty kilometres to and from a cleaning station. Added to this is the huge advantage of less residue, so higher yields. From a financial point of view, we don’t have to convince customers.”
Does the Mega-Inliner have any challenges?
”The only resistance we occasionally get is the remaining bag after unloading. Companies often initially think this is inconvenient. However, removing the bag from the tank is simple and companies are often quick to win over when they see how easy it is. Keeping in mind that the tank therefore does not need to be cleaned with all kinds of chemicals at a cleaning station afterwards. And the bag is recyclable.”
What is your company’s growth direction?
”Sustainability is of paramount importance to us, and with that we want to grow in a controlled way. This combined with food safety and quality assurance of the products we are able to transport. We want to grow in depth, more destinations, and in width through more product categories. First grow within Europe and then further into North America and further worldwide. We also want to move towards a system where companies can order our Mega-Inliner as a kind of Uber. By preventing cross-contamination with previous loads, it is easier to also bring back a filled tank with a different liquid after delivery. You’d be surprised how many empty tanks transport companies send on the road, more than half of them. We tackle that problem.”
What foods would you like to add to the range?
”We are developing a sterile coupler. With this, we are developing a sterile Mega-Inliner®. For short distances, tanks without a sterile coupling are now usually used. Dairy is a critical product and that requires a sterile process for long distances. For example, we get requests to transport dairy products from the Netherlands to Africa. Conventional carriers use sterile IBCs (intermediate bulk containers, ed.) of about 1,000 litres or drums of about 200 litres for such long distances and large quantities. With these, apart from all the handling and packaging costs, you can load a maximum of 10,000 litres per 20-foot container. In fact, there is simply no such thing as a 25,000-litre tank that can be made sterile. We will soon be able to do this with our Mega-Inliner, which is treated with gamma radiation as a sterile solution. So, by comparison, that’s 2.5 times more product transported per trip.”
Are you interested in the system or do you have a challenge, contact Coen our expert and we will make your supply chain more sustainable and efficient!
Source: Foodbusiness.nl
Mega-Inliner® is a combination of 2 everyday used bulk transport systems, we bring the best of these 2 worlds together for the best solution available on the market in transporting non-hazardous liquids. An environmentally conscious transport system that reduces Co2 emissions enormously and is also extremely cost-efficient. By using the Mega-Inliner System® planning becomes child’s play when connecting Inbound and Outbound flows.
- 100% product quality,
- No degradation
- No oxidation due to closed system when (un)loading
- No (de)saturation – carbonated products
- Temperature control (from -8c to 71c) , cooling or heating
- Lowest product spill/residue per load
- Lowest Co2 footprint possible per Mt product in total supply chain
- No cross-contamination
- No previous cargo restrictions
- No cleaning or rinsing of the tank, saving water, energy, and chemicals
- No empty kilometres or depot costs
- FDA & EU Food approved
- Halal & Kosher
- Mega-Inliner® 100% Recyclable (single source material)
- Aseptic loading, transport, and unloading possible
- Suitable for storage, longer shelf life
- One-man operation, short lead time
- No people on top of or in the tank.
- Connecting inbound and outbound logistics
Depending on the current supply chain we can be competitive with all. If you are transporting ready-to-drink in bottles now, the impact of using our system is huge, but changing the supply chain takes more time, switching from conventional tank container or flexitank to Mega-Inliner® is easy and gives you the benefits immediately. All other IBCs, Drums, kegs, etc are somewhere in the middle.
By using the Mega-Inliner® System it is possible to go directly to the next loading location without the need for cleaning between each load. Therefore, costs such as driver wages, cleaning costs and waiting time are being saved. Because there will be no residue left behind in the tank all costs of product being wasted are eliminated. Due to our Mega-Inliner®, your product will be shipped in a clean and closed environment and therefore there is no chance of cross-contamination or other problems.
By using the Mega-Inliner® System your Co2 emission will be reduced by a minimum of 30%. The Mega-Inliner® is 100% recyclable and cleaning of the Tank Container becomes obsolete. Our system makes it possible to connect Inbound and Outbound logistics by simply removing the Mega-Inliner® after each load, this results in no empty kilometres to and from cleaning stations, wastage of valuable (drinking) water belongs to the past (saving ± 2,500 litres per cleaning), no chemicals for cleaning are necessary. Ship your foodstuff or other non-hazardous liquids in bulk globally and pack locally save up to 60% on transport costs and reduce a minimum of 30% on your Co2 emission.