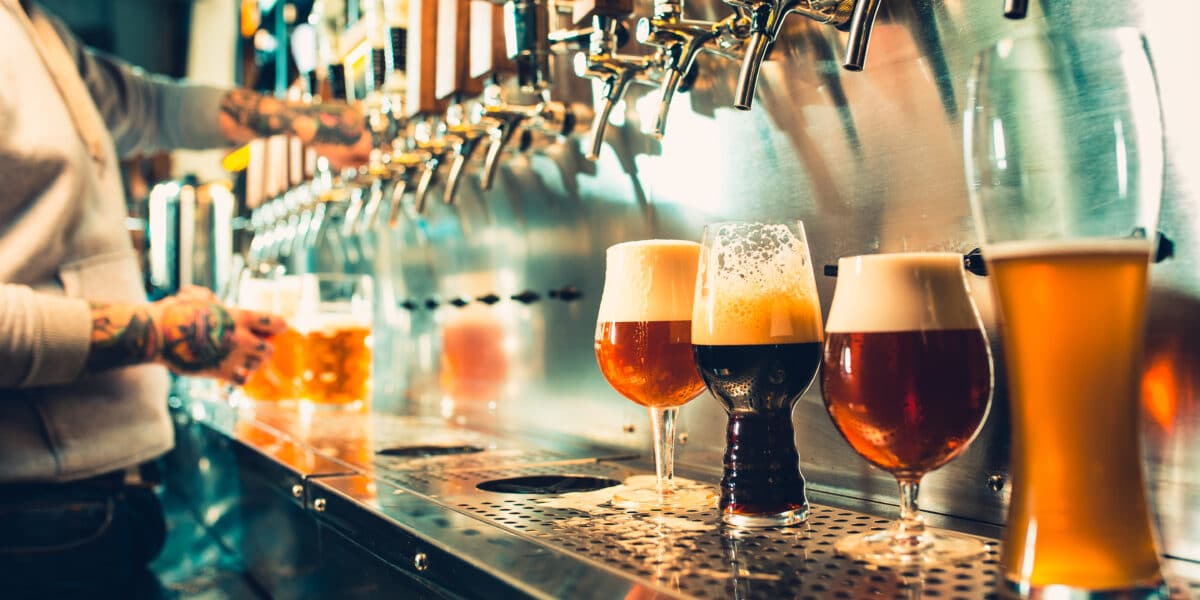
The Mega-Inliner® System is a combination of our 20ft. Mega-Inliner® Tank Container (MTC) combined with our patented Mega-Inliner® (Bag-in-tank). With each load a new Mega-Inliner® is installed, a one-man operation, easily installed within 5 minutes and easily removed within 15 minutes.
Want to know more about our system?
For the beer industry we provide different solutions:
- International/Domestic Transport
- Intercompany
- Hub and Spoke
- Events
Only Compressed Air
When transporting beer in a conventional tank container, it must not only be properly cleaned but also purged and pre-pressurized with Co2, during unloading CO2 is also needed. With our Mega-Inliner® this is no longer the case, thanks to our Mega-Inliner® the tank container does not need to be cleaned and CO2 is no longer needed, connect compressed air to our MTC and push the Mega-Inliner® completely empty at your desired destination without any risks of off-spec beer.
No foaming
When the beer is loaded into the Mega-Inliner®, foaming is eliminated. We utilize counter pressure (compressed air) when loading the tank container, and since the beer is filled in a closed environment (the Mega-Inliner®), foaming is impossible.
No quality loss
Because the Mega-Inliner® bag is a closed environment no oxygen can get into the product and no CO2 can escape, in addition, the beer will not be exposed to any metal or materials that will degrade the quality of the beer.
Ready to drink quality
When arriving at the destination the beer is still in perfect condition of CO2 and temperature, it can immediately be connected to a cellar beer delivery truck (hub and spoke), the bottling line, or a dispensing facility. Making your Supply Chain of beer far more efficient and sustainable.
Event solution, direct to tap
The Mega-Inliner® System can function as a keg with a capacity of up to 29,500 liters. By applying high-pressure compressed air (3 bar) on top of the Mega-Inliner® using our Mega-Inliner® Air Compressor, it can supply numerous taps with beer. The system does not use any CO2, making it superior, easier, safer, and more responsible than conventional systems.
Mega-Inliner® is a combination of 2 everyday used bulk transport systems, we bring the best of these 2 worlds together for the best solution available on the market in transporting non-hazardous liquids. An environmentally conscious transport system that reduces Co2 emissions enormously and is also extremely cost-efficient. By using the Mega-Inliner System® planning becomes child’s play when connecting Inbound and Outbound flows.
- 100% product quality,
- No degradation
- No oxidation due to closed system when (un)loading
- No (de)saturation – carbonated products
- Temperature control (from -8c to 71c) , cooling or heating
- Lowest product spill/residue per load
- Lowest Co2 footprint possible per Mt product in total supply chain
- No cross-contamination
- No previous cargo restrictions
- No cleaning or rinsing of the tank, saving water, energy, and chemicals
- No empty kilometres or depot costs
- FDA & EU Food approved
- Halal & Kosher
- Mega-Inliner® 100% Recyclable (single source material)
- Aseptic loading, transport, and unloading possible
- Suitable for storage, longer shelf life
- One-man operation, short lead time
- No people on top of or in the tank.
- Connecting inbound and outbound logistics
Depending on the current supply chain we can be competitive with all. If you are transporting ready-to-drink in bottles now, the impact of using our system is huge, but changing the supply chain takes more time, switching from conventional tank container or flexitank to Mega-Inliner® is easy and gives you the benefits immediately. All other IBCs, Drums, kegs, etc are somewhere in the middle.
By using the Mega-Inliner® System it is possible to go directly to the next loading location without the need for cleaning between each load. Therefore, costs such as driver wages, cleaning costs and waiting time are being saved. Because there will be no residue left behind in the tank all costs of product being wasted are eliminated. Due to our Mega-Inliner®, your product will be shipped in a clean and closed environment and therefore there is no chance of cross-contamination or other problems.
By using the Mega-Inliner® System your Co2 emission will be reduced by a minimum of 30%. The Mega-Inliner® is 100% recyclable and cleaning of the Tank Container becomes obsolete. Our system makes it possible to connect Inbound and Outbound logistics by simply removing the Mega-Inliner® after each load, this results in no empty kilometres to and from cleaning stations, wastage of valuable (drinking) water belongs to the past (saving ± 2,500 litres per cleaning), no chemicals for cleaning are necessary. Ship your foodstuff or other non-hazardous liquids in bulk globally and pack locally save up to 60% on transport costs and reduce a minimum of 30% on your Co2 emission.